利益を生みだすためには「売上高アップ」させるか又は「変動費・固定費のコストダウン」させる方法があります。それらの方法について、私どものコンサルティング事例の中より「変動費・固定費のコストダウン」事例をご紹介しましょう。
日本橋総合コンサルタント合同会社のホームページの構成を「サイトマップ」に表示して置きましたので、ページ閲覧の際にご活用頂けると幸いです。

生糸生産ラインの品質向上(歩留まり向上)
あるお客様は⽣の生産に新⽣産ラインを導入して⽴ち上げに苦慮していました。そこで私どもに「何とか早く生糸の新生産ラインを立ち上げたい」とのご要望がありました。
そこで、品質向上(歩留まり改善)対策を中心にして、管理監督者並びに作業員に対してQC活動を実施したところ、1年間で歩留まりが10%⇒80%まで向上しました。歩留まりは、原料や素材のインプット量に対して、実際に得られた部品・製品のアウトプット量の割合を意味しています。製造業にとって歩留まりは、生産性や効率性を示す重要な役割を果たし、歩留まりが高いほど原価が低減されます。この事例の場合、 歩留まりが10%⇒80%まで向上してますので、原価が大幅に下がっています。品質(歩留まり)を一定にかつ安定に維持するには作業者の教育が欠かせません。⽣産ラインの管理監督者の品質管理教育を⾏い、⾃前で品質の維持・管理及び歩留まり向上対策が実施できる様に教育しました。この結果、単に歩留まり向上しただけでなく、⽣⽷の⽣産量が安定的に増え、販路拡⼤にも繋がりました。
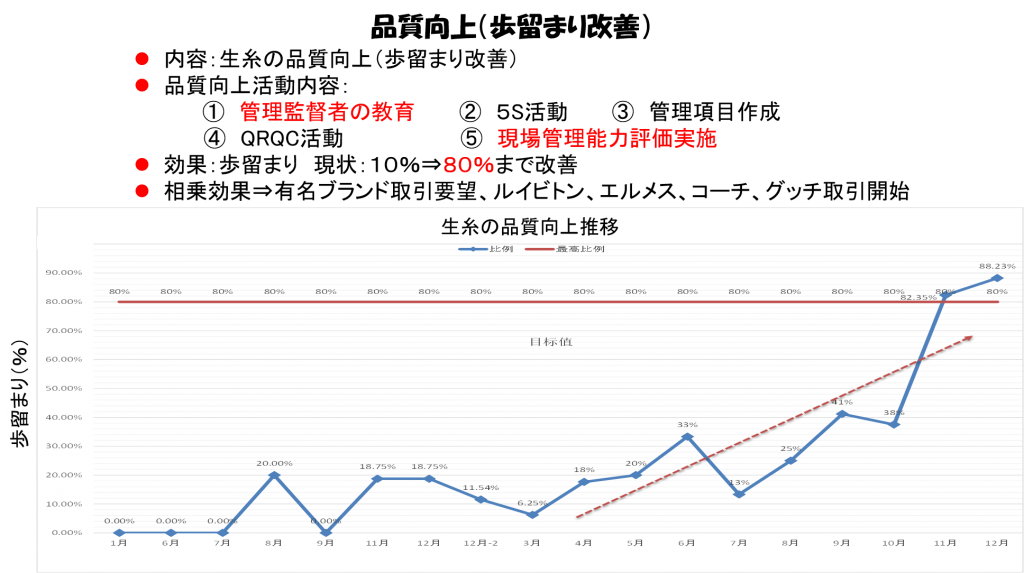
加工工程の⽣産性向上
製造業の⽣産ラインについてIE(経営⼯学)的な改善⼿法(⼯程分析・作業編成・⼯程改善・設備改善)を⽤いて、⽣産合理化を検討した結果、個別生産方式をセル生産方式に変えることにより、⼤幅な⼈員削減(工数削減)が可能となり、⽣産性向上を達成しました。
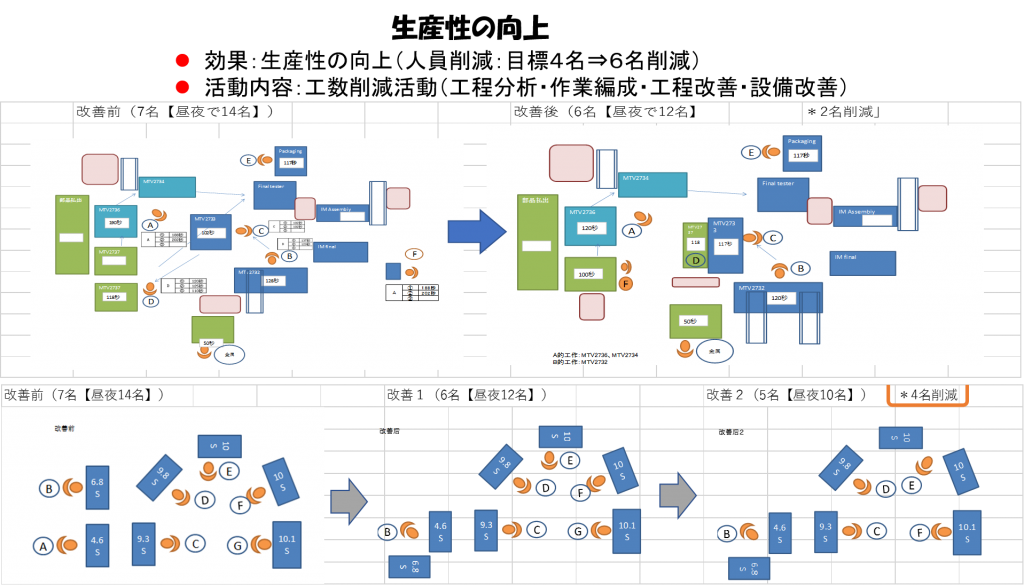
外注加工工程の内製化
ある素材加工専門製造メーカーからの依頼の事例です。経営者の方より「大手電機メーカーの下請けで、電気部品の素材を生産しており、素材に一部機械加工を施しお客様に納入している。素材加工の前工程を外注化している。外注による素材前工程の納期が2カ月と長いために、2か月分の素材を工程在庫を造っているが、工程在庫を造るための運転資金が逼迫しており、このままでは赤字になりそうだ。何とかして欲しい」とのご相談がありました。
外注加工の実態調査の結果(実際に外注先を訪問してます)、
- 前工程である素材切断~研磨工程の技術的な蓄積が無く、やむを得ず商社経由で素材切断~研磨工程を切断専門加工メーカーと研磨加工専門の加工メーカー5~6社に外注加工を依頼しており、最終検査は商社で行ってた。
- 外注加工ルートが複雑であり、その結果納期が約2か月と長く、納入先へのデリバリーを守るためには2カ月分の回転在庫を確保する必要があった。
- 納期管理・品質管理面で問題が山積みであった。
- 外注におけるコストダウンの可能性は、1~2%/年であり、大幅なコストダウンは望めなかった
- 外注加工の技術レベルは予想以上に低く、加工工程の工程設計を十分に行えば、自社内で素材切断~研磨工程の前工程を内製化できることが分かった。
そこで内製化に際して必要な切断加工技術・研磨技術を構築して、内製化を図ったところ、
- 回転在庫を2カ月から2週間に短縮できた。
- 品質の向上及び安定化が可能となった。
- 大幅なコストダウンが可能となった。
以下に外注加工の内製化に伴う工程プロセスの変更事例を示しておきます。
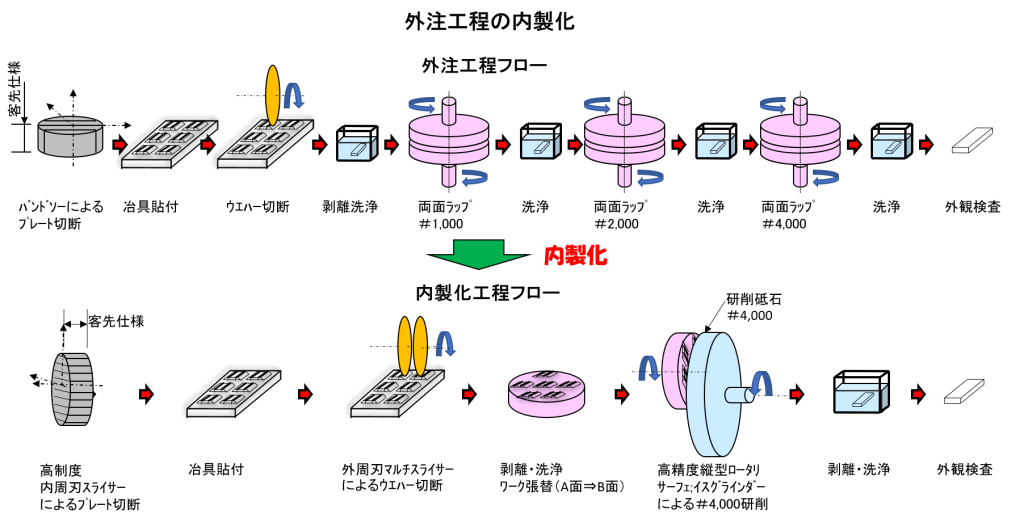
外注化にはメリット・デメリットがありますので、これらを考量した上で外注化を行うことが望ましいと言えます。
メリット | デメリット |
外部の知見や技術を活用でき、自社の弱点を補うことができる | マネジメントコストが発生し、コストアップとなる可能性がある |
増産に対して人員増が不要で、再教育の手間が省ける | 意思伝達が困難で、品質管理が不十分となる可能性がある、 |
人件費や設備費などの固定費を節約できる | 外注先の繁忙期によってはいつでも仕事を発注できるとは限らない |
機密漏洩の危険性も想定される |
物流コストの削減方法
物流コストとは、物流業務において物を移動させるためにかかる費用の総称です。物流コストは、輸送・運送費、荷役費、保管費、管理費や人件費、ピッキング、包装費等に分類できます。これら物流コストの中で輸送・運送費が一番コストが嵩みます。荷役費は輸送・運送の際の補助作業で当然の作業と思われており物流コストと認識されていないように思われます。そこで本節では、輸送・運送費及び荷役費に的を絞り、これら費用のコストダウン方法について考えて見ましょう。
(1)輸送・運送費
商品を運搬するときに発生する費用を輸送費と呼びます。配送を外部業者に委託する場合には、仕様・最大積載量・輸送距離などによって運送費が決まりますし、商品を届ける宅配便等の「小口配送料金」、海外や国内各地に商品を送るために発生する「航空便・船便・貨物鉄道などの配送料金」なども運送費に含まれます。
自社便を使用する際には、ガソリン料金・高速料金や車両の減価償却費なども輸送費に該当します。。
自社便で配送する際には、
- ガソリン代金・高速代金を考慮して配送ルートを短くするようにする
- 積載率を高め1回で輸送できる量を多くする
- 配送車への積み込みや配送車からの積み下ろし作業を短時間でできるようにする
等の工夫が必要となります。
(2)荷役費
原材料を購入の際には原材料メーカーがトラックヤードから原材料倉庫まで運搬します。運送を外注化している場合には、商品倉庫からトラックへの積み込み作業は外注先の配送者(運転手)で行うのが一般的です。
自社便で客先への運送を行う場合には、商品倉庫からトラックヤードへの構内運搬及び積み込み作業、客先への輸送及び客先での積み下ろし作業も自社で行い、作業量に応じて時間がかかればそれだけ人件費もかさみます。事前に商品倉庫内でのピッキングや仕分けを十分に行っておく必要があります。
荷役費用の削減によるコストダウン方法及び事例を以下に示しておきます。ご参考にして頂けると幸いです。
(3)コンサルティング事例
1)商品倉庫の5S
商品の搬入・搬出を容易にし商品管理コストを下げるために商品倉庫の5Sを実施した事例です。倉庫内が乱雑な状態であったり商品のがどこにあるか探し廻ることが多々ありました。商品の番地を決め置き方も工夫したことにより、商品の搬出・搬入に伴う時間を短縮するとともに商品管理が容易となりました。
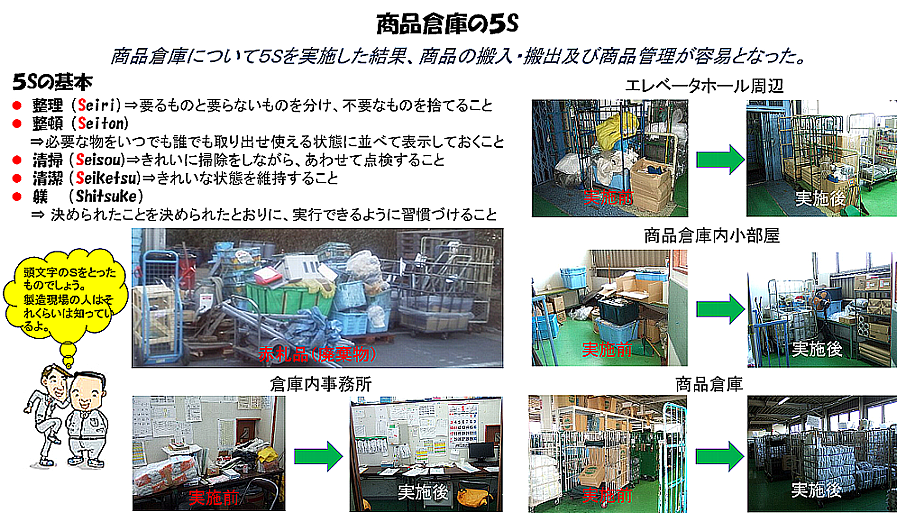
2)マテハン分析
マテハン分析とは、「マテリアル・ハンドリング(Material Handling)分析」の略称で「運搬分析」とも呼ばれており、先ほどご紹介したIE分析手法の一つです。マテハン分析には「運搬分析」・「運搬活性化分析」及び「カラ運搬分析」などの手法があります。ここでは「運搬活性化分析」を取り上げて、自社内での荷下ろし・積み替え・移動・出荷作業などのコストを下げる工夫について検討して見ましょう。この方法は製造業のみならず、あらゆる業界において製品・商品の搬入・搬出及び運搬時の管理コストを低減させる時の基本的な考え方となっています。
モノの荷姿の原則に基づき、
- 荷姿の標準化
- パレット化
- 再取り扱の排除
を行い、運搬活性化指数を低減させることにより、運搬作業時間を3割改善することが可能となります。
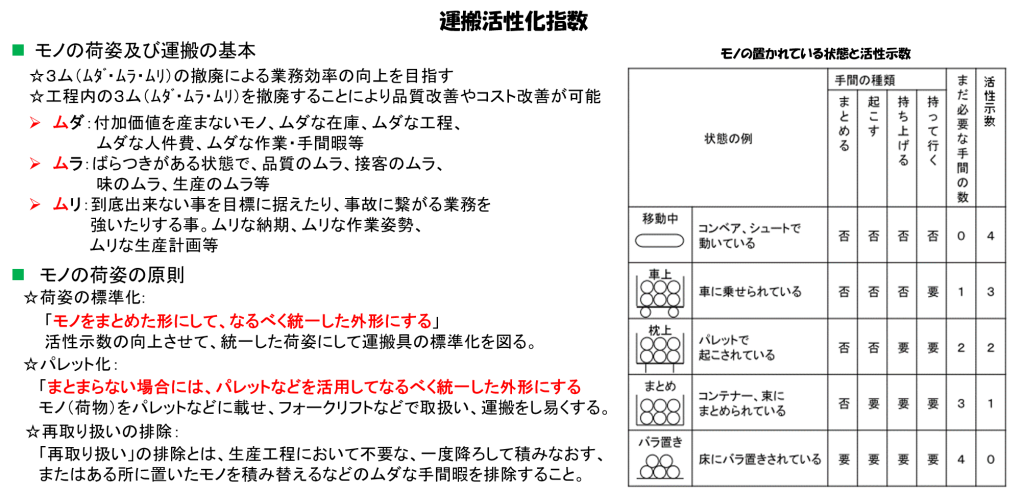
① マテハン分析結果の事例
下記の図表はある製造メーカーにおけるマテハン分析結果の事例を示しています。
社内ではコンテナーを使って品物の搬送を行っていますが、品物の搬入・搬出時には、コンテナー・袋詰めやドラム缶等を使っており、客先によって荷姿がバラバラです。各荷姿の時の活性化指数は、
・ビニール袋・台車積送品・・・・・活性化指数=3.1
入荷時にビニール袋からコンテナーに品物の移し替え、出荷時にコンテナーからビニール袋詰めを行います。
・コンテナー・パレット積載品・・・活性化指数=2.7
入・出荷用コンテナーを社内搬送用コンテナーとして使用可能ですので、品物の移し替えはありません。
・ドラム缶制裁品・・・・・・・・・活性化指数=2.4
入・出荷時にドラム缶⇔社内用コンテナーに移し替える手間暇がかかります。
➁ 活性指数向上のための留意点
この製造メーカーで活性化指数を向上させるための施策として、
- 製品の入出荷時及び工程内の搬送は全てコンテナー・パレット積載方式としたい
- コンテナー積載品は直置きを避け、パレット上に積載管理する
- ドラム缶詰めは極力避る様にお客様と交渉し、コンテナー・パレット積載方式に改める
事などがが考えられ、経営者の方に提言・実行して貰いました。。
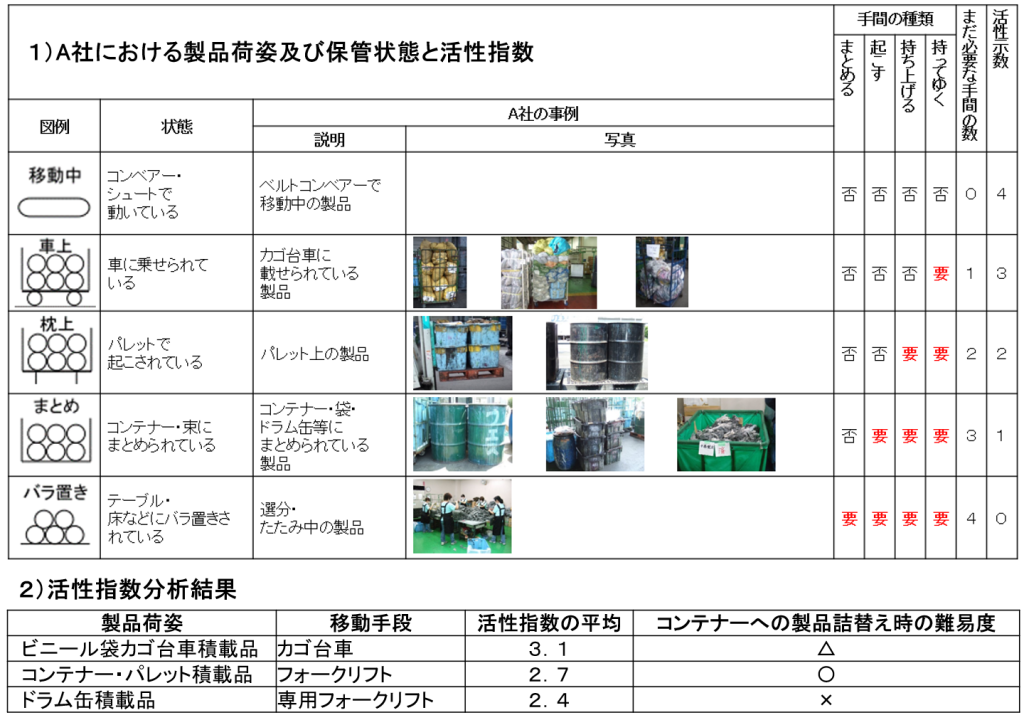

このページに関するご質問・お問い合わせはお問い合わせフォームにてお願いします。
「利益を生み出す」ページは下記に示す主テーマで構成されております。
- 利益を生み出す・・・本ページ
- 利益を生み出す管理会計
- 管理会計に基づく変動損益計算書
- 売上高アップ
- 変動費削減によるコストダウン
- 固定費削減によるコストダウン
- 業務改善・生産性向上事例のご紹介・・・本ページ
『利益を生み出す』ページを構成する具体的なテーマにつきましては、上記主テーマ一覧と画面右側のサイドメニューに表示しております。続きについては主テーマ一覧もしくはサイドメニューのテーマをクリックして御覧いただけると幸いです。
